Why spreadsheets are still your biggest compliance risk in fleet management
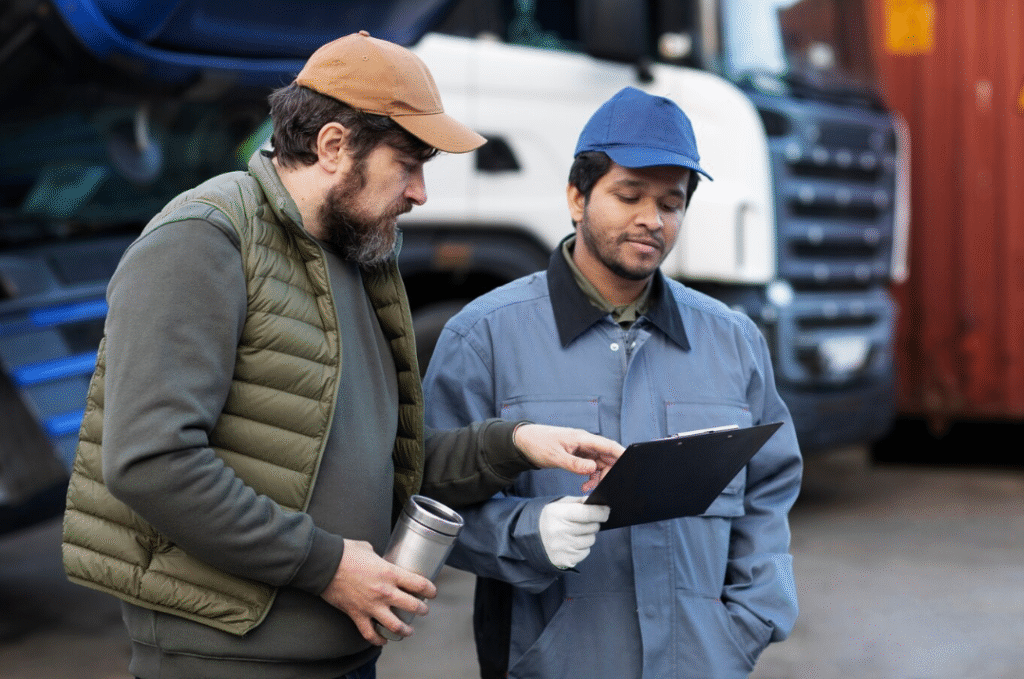
In the world of fleet maintenance and compliance, spreadsheets have long been a default tool. They’re familiar, flexible, and seemingly low-cost. But for growing fleets and regulated operations, that familiarity masks a serious problem: spreadsheets are silently introducing risk. Not just operational inefficiency or missed maintenance tasks, but genuine compliance risk that can cost businesses time, money, and in some cases, their licenses.
If you’re a fleet operator still relying on spreadsheets to manage maintenance, inspections, repairs, and compliance documentation, it’s time for a reality check. Here’s why.
Spreadsheets are not built for fleet compliance
At their core, spreadsheets are general-purpose tools. They’re not built to understand the nuances of DOT regulations, Canadian CVOR requirements, or province-specific inspection schedules. There are no alerts when a registration is due. No automatic escalation when a fault is flagged. No traceable audit trail.
Fleet compliance is a live process. Auditors don’t just want to see data – they want to see workflows, alerts, response times, and resolution history. A spreadsheet, even a carefully maintained one, can’t deliver that level of operational transparency.
Human error is inevitable
Manual data entry is at the heart of spreadsheet use. But humans aren’t built for perfect accuracy. One wrong digit in an odometer entry, one missed date on a service schedule, one duplicated record – and the consequences ripple across your operation.
In regulated fleets, errors like these can trigger a failed audit, a missed inspection, or even a preventable roadside breakdown. A spreadsheet won’t warn you when data is inconsistent. Gearbox will.
No real-time visibility
Fleet operations move fast. Assets are in the field. Faults happen. Inspections expire. Repairs are delayed. Spreadsheets operate on lag – they’re only as up-to-date as the last person who opened the file.
That lag means your compliance status is always out of date. In contrast, a platform like Gearbox gives you real-time asset status, with live updates from Prestart apps, work orders, and service calendars. When your asset compliance depends on up-to-the-minute accuracy, spreadsheets simply can’t compete.
Audits become a paper chase
One of the biggest headaches for any compliance manager is preparing for an audit. With spreadsheets, that usually means hunting down documents, printing maintenance logs, cross-referencing records, and hoping nothing has been overlooked.
With Gearbox, all your maintenance and compliance data lives in one system. Every asset has a digital history. Job cards are traceable. Fault reports are logged. Contractor documents, risk assessments, permits – all filed and accessible. Instead of scrambling to prepare, you walk into the audit ready.
Poor accountability and oversight
Spreadsheets don’t track who made changes. They don’t time-stamp approvals or record escalation history. In a regulated environment, that lack of accountability is a major blind spot.
Compliance isn’t just about checking the boxes. It’s about demonstrating control. Gearbox provides full traceability – who flagged a fault, who approved the work order, who closed the inspection. That accountability protects you during legal reviews, investigations, and internal audits.
No alerting or automation
Spreadsheets are passive. They don’t tell you what needs attention. They don’t flag overdue services or alert you when a medical certificate is about to expire. You have to look for problems manually.
Gearbox flips that. Its alerting engine monitors registrations, services, repairs, inspections, employee training, medicals, and more. Daily summaries hit your inbox. Prestart faults trigger instant emails. The system works for you – not the other way around.
Scaling becomes impossible
The more assets you manage, the harder it is to scale a spreadsheet system. Eventually, someone becomes the “spreadsheet owner” – and your entire compliance infrastructure depends on them.
As your fleet grows, Gearbox grows with you. Whether you manage 50 or 5,000 assets, the system handles it with structured workflows, permission controls, contractor tracking, and multisite support. There’s no single point of failure.
Missed cost savings
Spreadsheets don’t help you make decisions. They don’t tell you which assets are consistently high maintenance. They don’t flag which repairs are under warranty. They can’t show you which parts are driving your costs up.
Gearbox turns your operational data into insight. It highlights trends, inefficiencies, and opportunities to extend asset life or cut down on admin time. The result? Reduced costs and increased uptime.
What the alternative looks like
Thousands of operators have already made the switch from spreadsheets to dedicated fleet maintenance software. Gearbox users gain:
- Real-time asset status with visual traffic lights
- Digital maintenance history for every vehicle and asset
- Automated service scheduling based on miles, hours, or time
- Fault reporting integrated with pre-trip checks
- Centralized contractor documentation and expiry tracking
- Load sheet tracking and compliance documentation
- Configurable compliance reviews
They also gain peace of mind. Knowing that when an audit comes, the system has them covered.
The longer you wait to replace spreadsheets, the more risk you’re carrying. Risk of audit failure. Risk of missed services. Risk of non-compliance. Risk of inefficiency. The fix isn’t complicated – and it’s already been proven across construction, agriculture, municipal, intermodal, and cold chain fleets.
Spreadsheets were never built for this job. Gearbox is.
Want to learn how your operation compares? We’ll walk you through how other fleets like yours are using Gearbox to stay compliant and stay ahead. Book a demo.